- Home
- HDPE Pipe
HDPE Pipe
Discover our premium range of HDPE pipe, designed for durability, efficiency, and environmental sustainability. Renowned for its robustness, our HDPE pipe offers unparalleled reliability and longevity in various industrial, municipal, and residential applications. Our blue HDPE pipe (suitable for potable water and other underground applications) and black HDPE pipe (for non-potable water and above-ground applications) are available in sizes 90mm, 110mm, 125mm, 160mm and 180mm. Our HDPE pipe is available in coils of 50m and 100m and lengths of 6m.
What is the difference between MDPE and HDPE pipe?
High-Density Polyethylene (HDPE) and Medium-Density Polyethylene (MDPE) are both types of polyethylene pipes used in various applications, including water and gas distribution, sewage systems, and irrigation. While they share some similarities, there are key differences in their properties and applications:
Density and Material Structure:
HDPE: High-Density Polyethylene has a density range of 0.941-0.965 g/cm³. It is made from petroleum and has a more linear structure with fewer side branches, providing higher tensile strength and temperature resistance.
MDPE: Medium-Density Polyethylene has a density range of 0.926-0.940 g/cm³. It has more branching than HDPE, which gives it a more compact molecular structure and makes it less rigid.
Flexibility and Stress Resistance:
HDPE: Due to its higher density, HDPE pipe is less flexible compared to MDPE. However, this rigidity provides higher resistance to stress cracking. HDPE pipes are often used in high-pressure applications.
MDPE: MDPE offers better stress cracking resistance than HDPE pipe because of its higher flexibility and lower density. It's more suitable for applications where the material is subject to external forces that could cause bending and flexing.
Durability and Chemical Resistance:
Both HDPE and MDPE have excellent resistance to most common chemicals and are not affected by corrosion or electrochemical reactions, making them suitable for various piping applications. However, HDPE's higher density gives it a slight edge in environments where chemical resistance is critical.
Temperature Resistance:
HDPE: It can withstand higher temperatures compared to MDPE. HDPE's melting point is around 130°C, making it suitable for applications where the pipes might be exposed to higher temperatures.
MDPE: It has a lower heat resistance than HDPE and is more suited for cold water applications.
Applications:
HDPE: Used in more demanding environments and applications such as water and gas mains, sewer systems, industrial piping, and even in mining. It is preferred where high pressure and temperature resistance are required.
MDPE: Commonly used for gas distribution networks, potable water supply, and other medium-pressure applications. It is favoured in situations where flexibility and ease of installation are important.
How do you cut HDPE pipe?
To ensure a straight and clean cut, we recommend using a large-diameter pipe cutter such as the Nerrad Professional Wheel Pipe Cutter which can handle pipe diameters up to 170mm.
Here's a step-by-step guide on how to use a wheel pipe cutter:
- Select the Correct Cutter: Make sure the wheel pipe cutter you are using is suitable for the diameter and material of the pipe you intend to cut.
- Inspect the Cutter: Before you begin, inspect the cutting wheel and the adjustment mechanism to ensure they are in good condition. The cutting wheel should be sharp and free of any damage.
- Mark the Pipe: Measure and mark the exact location where you want to cut the pipe. Ensure the mark is straight and clear.
- Open the Cutter: Loosen the adjustment knob to open the cutter jaws wide enough to fit around the pipe.
- Position the Cutter: Place the cutter on the pipe so that the cutting wheel aligns with the mark you've made. The pipe should be snugly seated between the cutting wheel and the rollers.
- Tighten the Cutter: Gently tighten the adjustment knob until the cutting wheel makes firm contact with the pipe. Avoid over-tightening, as this can deform the pipe or damage the tool.
- Rotate the Cutter: Hold the pipe steady with one hand and rotate the cutter around the pipe with the other hand. After each complete rotation, slightly tighten the adjustment knob to bring the cutting wheel progressively deeper into the pipe material.
- Repeat the Process: Continue rotating the cutter and tightening the knob incrementally after every few rotations. It's important to apply consistent pressure and not rush the process, as a clean cut depends on gradual, steady progress.
- Complete the Cut: Continue the cutting process until the pipe is severed. You should feel a sudden ease in resistance when the cut is complete.
- Inspect and Deburr: Once the pipe is cut, remove any burrs or sharp edges from the inside and outside of the cut end using a deburring tool or a file. This step is crucial for preparing the pipe for a clean, leak-free connection.
How do you join HDPE pipe?
Joining HDPE (High-Density Polyethylene) pipe requires specific techniques to ensure a durable and leak-proof system. The most common methods for joining HDPE pipes include butt fusion, electrofusion, and using mechanical fittings. Here's an overview of how these methods are applied:
- Butt Fusion: Butt fusion is a popular method for joining HDPE pipes, especially for larger diameters. This method involves heating the ends of two pipe segments and pressing them together.
- Prepare the Pipe Ends: Clean and square-cut the pipe ends to be joined. Remove any dirt, grease, or other contaminants.
- Align and Clamp: Secure the pipe ends in the fusion machine clamps and align them.
- Heat the Pipe Ends: Use a heated plate to heat the pipe ends to the recommended temperature. Once the proper melt pattern is achieved, remove the heating plate.
- Join the Pipe Ends: Quickly bring the two pipe ends together under a controlled force. Maintain the force until the joint cools and solidifies.
- Electrofusion: Electrofusion is ideal for repairs and fittings, particularly in tight spaces where a fusion machine can't be used. It involves using a fitting with embedded heating elements.
- Prepare the Pipe Surface: Clean the pipe surface and scrape it to expose fresh material. Mark the insertion depth on the pipe.
- Insert the Pipe into the Fitting: Slide the electrofusion fitting onto the pipe end, ensuring it reaches the marked depth.
- Apply Electric Current: Connect the electrofusion fitting to an electrofusion processor, which applies an electric current, causing the internal coils to heat and fuse the pipe and fitting together.
- Cooling Period: Allow the joint to cool down for the specified time before handling or pressurising the pipeline.
- Mechanical Fittings (up to 125mm): Mechanical fittings offer a quick and straightforward method for connecting HDPE pipes, suitable for both temporary and permanent installations.
- Prepare the Pipe End: Ensure the pipe end is clean and cut squarely.
- Insert the Pipe: Insert the pipe end into the mechanical fitting. Depending on the fitting design, it may have a compression ring, gasket, or other sealing mechanism.
- Tighten the Fitting: Tighten the fitting according to the manufacturer's instructions to secure the pipe. This usually involves tightening bolts or screws to compress the gasket or seal inside the fitting against the pipe.
For all methods, it's crucial to follow the manufacturer's specific instructions regarding temperatures, pressures, and cooling times to ensure a strong and effective joint. Additionally, using proper safety equipment and ensuring a clean working environment are essential for a successful HDPE pipe installation.
Is HDPE pipe suitable for drinking water?
Yes, our blue HDPE pipe is WRAS and BS EN 12201 approved making it suitable for use with potable water. The blue colour is a standard industry code that signifies the pipe is designed for potable water applications. Here's why blue HDPE pipe is suitable for drinking water:
Colour Coding: The blue colour is used to differentiate potable water lines from pipes used for other purposes, such as sewage or irrigation. This colour coding helps prevent cross-contamination during installation and maintenance.
Material Safety: HDPE is a non-toxic material that is resistant to the buildup of bacteria and other microorganisms. It does not leach harmful substances into the water, making it safe for transporting drinking water.
Corrosion Resistance: HDPE is inherently resistant to corrosion and does not rust, degrade, or corrode when exposed to water. This feature helps maintain water quality over time.
Chemical Resistance: It is resistant to many chemicals, ensuring that the water quality is not compromised by external contaminants.
Durability: HDPE pipes are known for their strength, flexibility, and durability. They can withstand high pressure and harsh environmental conditions, reducing the risk of leaks and breaks.
Certification: In the UK, any pipe used for potable water supply must meet stringent standards to ensure it is safe for drinking water applications. Blue HDPE pipes are required to comply with UK standards such as BS EN 12201 for plastic piping systems and WRAS (Water Regulations Advisory Scheme) guidelines. WRAS approval indicates that the pipe material does not affect water quality or pose a health risk. These certifications confirm that the blue HDPE pipes are suitable for transporting drinking water, as they have been tested and approved for their safety, quality, and performance in accordance with UK regulations. Always ensure that HDPE pipes for drinking water are certified to these standards to guarantee their appropriateness for potable water use in the UK.
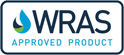
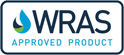


Can you glue HDPE pipe?
No. Gluing HDPE (High-Density Polyethylene) pipe using conventional adhesives is ineffective because HDPE is a thermoplastic with a non-polar surface that resists most types of chemical adhesives. Traditional glues that work well with other plastics or materials typically do not adhere to HDPE due to its high chemical and solvent resistance, and its smooth, non-porous surface.
HDPE Pipe Sizing & Ratings
MDPE Pipe Dimensions, Metric, BS EN 15494:2003 |
||||||
Pipe Size (mm) | Average Bore Inside Diameter (mm) | Average Wall Thickness (mm) | Approximate Weight per Metre (kg) | PE Rating | SDR Rating | Pressure Rating (bar) |
90 | 78.7 | 5.7 | 1.39 | 100 | 17 | 10 |
110 | 96.3 | 6.9 | 2.06 | 100 | 17 | 10 |
125 | 109.5 | 7.8 | 2.66 | 100 | 17 | 10 |
160 | 140.3 | 9.8 | 4.38 | 100 | 17 | 10 |
180 | 158.0 | 11.0 | 5.49 | 100 | 17 | 10 |
If you require any further information, our excellent customer service team is here to help so please call us on 01794 835835.