- Home
- Actuated Valves
Actuated Valves
What is an Actuated Valve?
An actuator valve is a valve that is operated by an actuator. The actuator is a device that uses an external power source to move or control a mechanism or system. In the context of valves, actuators are used to control the position of the valve, thereby regulating the flow of a fluid (liquid or gas) through a pipeline. Actuator valves can be electric, pneumatic, hydraulic, or manual, each type being suited for different applications and operational environments. Electric actuators use electrical energy to create motion, pneumatic actuators use compressed air, hydraulic actuators use hydraulic fluid, and manual actuators rely on human intervention.
How Does an Actuated Valve Work?
The working principle of an actuator valve varies based on the type of actuator:
- Electric Actuators: Electric actuators use an electric motor to drive a mechanism that opens or closes the valve. The motor's rotational motion is converted into linear motion by a gearbox and a drive mechanism. This type of actuator is known for its precision and ability to integrate with automated control systems, making it ideal for applications requiring accurate flow control​​​​.
- Pneumatic Actuators: Pneumatic actuators use compressed air to generate the force needed to move the valve. The compressed air acts on a diaphragm or piston, which moves the valve stem to open or close the valve. Pneumatic actuators are valued for their rapid response times and are commonly used in environments where electric actuators might pose a risk, such as in hazardous or explosive atmospheres​​​​.
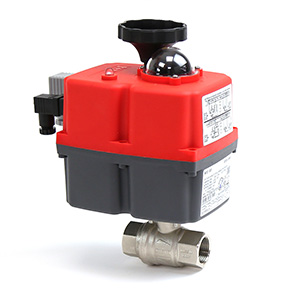
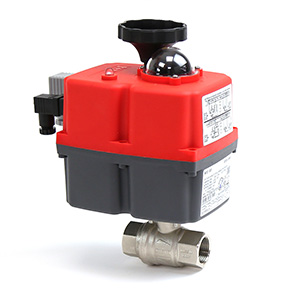
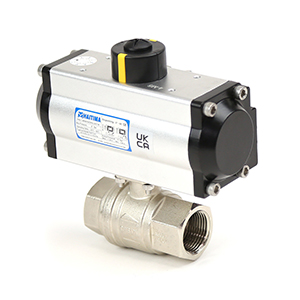
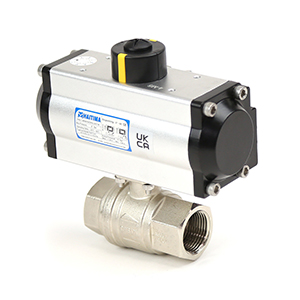
What are the Advantages and Disadvantages of Electric and Pneumatic Actuators?
- Electric Actuators: Advantages include high precision, reliable operation, and easy integration with control systems. Disadvantages are higher cost and the need for a continuous power supply.
- Pneumatic Actuators: Advantages include cost-effectiveness, fast response times, and suitability for hazardous environments. Disadvantages are lower precision compared to electric actuators and the need for a compressed air supply​​​​.
What Factors Should be Considered When Selecting a Valve Actuator?
Selecting the right valve actuator is crucial for ensuring the optimal performance and reliability of a fluid control system. Several factors need to be carefully evaluated to match the actuator to the specific application requirements. Here is a detailed guide on the key considerations:
- Torque and Force Requirements
- Torque Requirement: Determine the amount of torque needed to operate the valve. This includes the breakaway torque (to start moving the valve), running torque (to keep the valve moving), and seating torque (to fully close the valve).
- Valve Type and Size: Different types of valves (e.g., ball valves, butterfly valves) and sizes have varying torque requirements. Larger valves typically need more torque to operate.
- Differential Pressure: The pressure difference across the valve can significantly affect the required torque. Higher differential pressures generally increase torque requirements​​​​.
- Operating Environment
- Temperature: The ambient and operating temperatures can impact actuator performance. Some actuators are designed to operate in extreme temperatures, whether very high or very low​​​​.
- Corrosive and Hazardous Environments: For environments that are corrosive or potentially explosive, actuators must be constructed from materials that resist corrosion and meet safety certifications (e.g., ATEX, NEMA standards).
- Ingress Protection: The actuator's enclosure should provide adequate protection against dust, moisture, and other environmental factors, often specified by IP ratings​.
- Power Supply and Control Systems
- Power Source: The type of actuator (electric, pneumatic, hydraulic) depends on the available power source. Electric actuators need a power supply, pneumatic actuators require compressed air, and hydraulic actuators use pressurized fluid​​​​.
- Control Integration: Ensure the actuator is compatible with the control system. This includes considerations for control signals, feedback mechanisms, and communication protocols. Advanced actuators might offer integration with digital control systems and provide diagnostic data​​​​.
- Fail-Safe and Emergency Operations
- Fail-Safe Requirements: Determine if the actuator needs to default to a specific position (open or closed) in the event of a power failure. This is crucial for maintaining safety and process control in critical applications​​​​.
- Manual Override: Some applications may require the ability to manually operate the valve in case of actuator failure. Ensure the actuator design includes a manual override feature if needed.
- Speed of Operation
- Cycle Speed: The speed at which the valve needs to open or close can affect the choice of actuator. Pneumatic actuators are often preferred for faster cycle times, whereas electric actuators provide more precise control but might operate slower​​.
- Duty Cycle: Consider the actuator's duty cycle, which is the frequency of operation over a given period. High-cycle applications require actuators designed for frequent operation without overheating or excessive wear​​.
- Mechanical Compatibility
- Mounting and Interface: Ensure the actuator can be properly mounted to the valve. Standardized mounting interfaces (e.g., ISO 5211) help ensure compatibility between the actuator and the valve.
- Rotational Requirements: Determine the necessary rotation for valve operation. Some valves require a 90-degree turn, while others might need multiple turns. Select an actuator that matches these rotational requirements​​​​.
- Maintenance and Lifecycle Costs
- Initial and Ongoing Costs: Consider both the initial cost of the actuator and the long-term maintenance costs. Electric actuators might have higher upfront costs but lower maintenance, while pneumatic actuators might be cheaper initially but require regular air supply maintenance​​​​.
- Reliability and Durability: Choose actuators from reputable manufacturers known for reliability and durability. This ensures lower maintenance and longer operational life, reducing total cost of ownership.
- Application-Specific Requirements
- Application Type: Different applications (e.g., chemical processing, water treatment, oil and gas) have specific requirements that influence the choice of actuator. For instance, actuators used in food and beverage industries might need to meet sanitary standards​​​​.
- Safety and Regulatory Compliance: Ensure the selected actuator complies with all relevant safety and regulatory standards for the specific application and industry​​.
What Applications are Actuated Valves Commonly Used For?
Actuated valves are used in a wide range of industries, including water treatment, chemical processing, HVAC systems, oil and gas, and food and beverage production. They are essential for processes requiring precise control over fluid flow, automated operation, and reliable performance in various industrial environments​​​​.
If you require any further information, our excellent customer service team is here to help so please call us on 01794 835835.